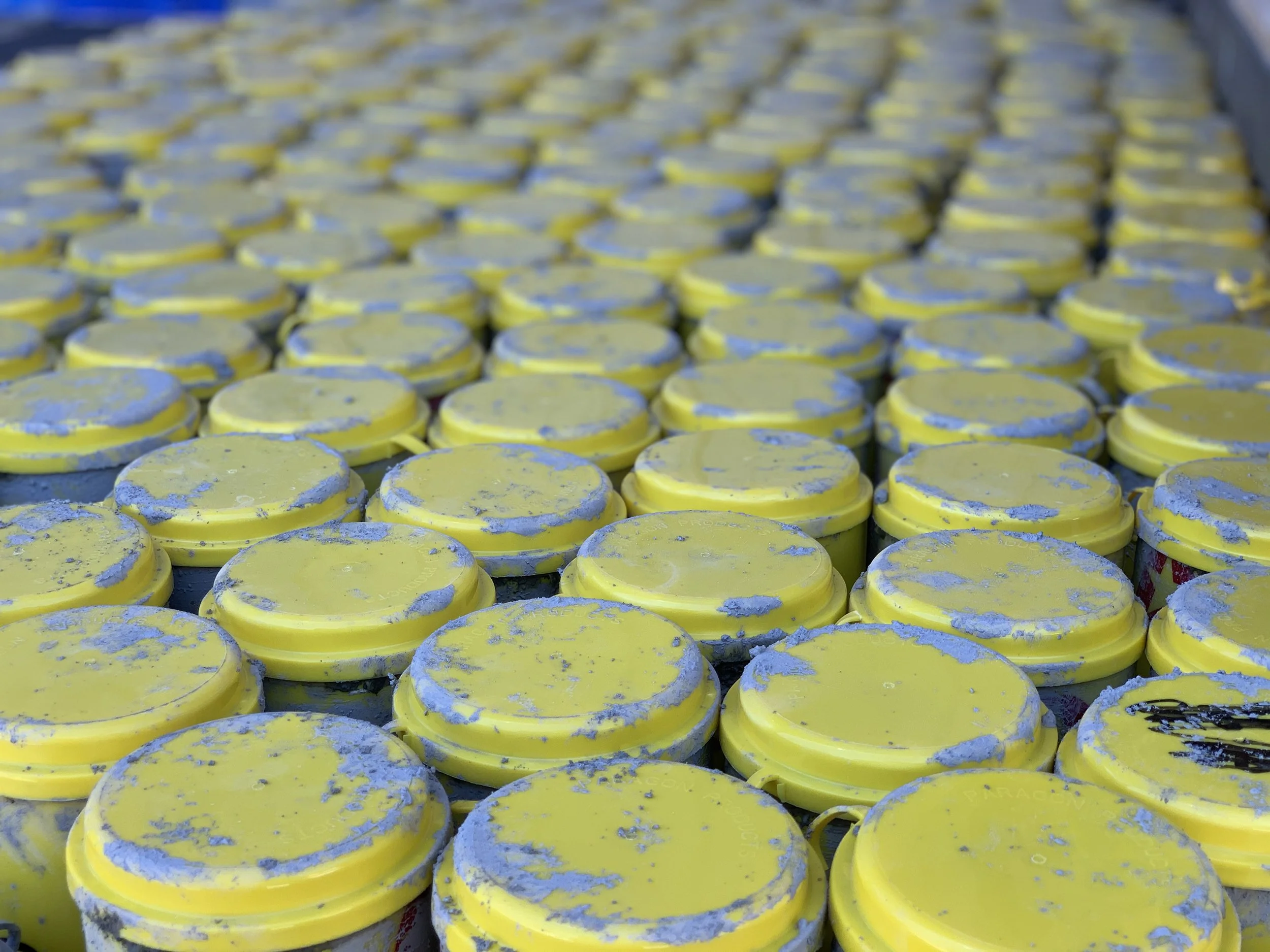
Created in the field by a concrete finisher, E5® Nano Silica continues to strengthen our concrete industry.
Unlike all other admixtures in the concrete industry, E5® Nano Silica Products were developed and refined in the field, not in a lab under perfect conditions. It has taken decades for the concrete industry to adopt this new technology and learn of it’s particle packing power using nano technology to fill voids and create dense, sustainable concrete.
We invite you to explore what we have learned below about this powerful material we call E5® Nano Silica.
-
E5® products chemically bind nano-silica in concrete at the initial reaction point – internally curing concrete. E5® products create stronger, more durable concrete that resists chemical and physical attack while significantly reducing the carbon footprint of construction projects.
-
E5® products help concrete realize its maximum potential with an efficient, economical, and sustainable process. E5® products improve durability, finishibility, and workability while reducing cracking, chloride ingress, shrinkage, and curling – all of which extend the concrete’s service life.
Poor field curing, along with concrete’s inability to fully cure, has robbed the industry of concrete’s maximum potential. E5® products control water loss and create up to 30% greater cement hydration efficiency – something conventional curing can not accomplish.
-
E5® products eliminate the need for traditional curing methods. Contractors gain immediate access for construction, saving up to 7 days over wet curing requirements. Costly and time-consuming removal of topically applied membranes is eliminated, maintaining warranty compliance for flooring. Concrete workability is improved, facilitating greater production capacity and improved finished quality.
-
Construction projects all across the US have benefited from using E5® Nano Silica Solutions. From flatwork to infrastructure, E5® Nano Silica is designed to be used in every yard of concrete.
-
Concrete is one of the most common and reliable construction materials in the world and is composed of cement, water, sand, and rock. The importance of water to aid the finishing of concrete is well known in the concrete and construction industry. As a result, it has been common practice to supply water on the surface of the concrete to create a creamy concrete that is easier to work with. More recently, internal curing has been utilized to hydrate the concrete after it is set. So what is internal curing and how can it be used to improve concrete?
The American Concrete Institute in 2018 defined internal curing as “supplying water throughout a freshly placed cementitious mixture using reservoirs, via pre-wetted lightweight aggregates, that readily release water as needed for hydration or to replace moisture lost through evaporation or self-desiccation” (American Concrete Institute, 2018). The goal of internal curing is to prevent water from leaving the concrete.
As water leaves the concrete, several negative effects are observed including bleed channels which result in excess bleed water at the top of the surface. As the concrete begins to set, excess water migrates through the porous cementitious matrix leaving open channels within the concrete surface and subsurface. These channels allow for harmful chemical agents from the environment to leach into the concrete and reduce the strength and durability of the concrete structure. Additionally, the water leaving the concrete is necessary for proper hydration of the concrete mixture. Internal curing not only helps to prevent the bleeding of water through concrete, but it also allows water to penetrate deeper into the concrete mixture.
E5® Internal Cure alters the back-bone of concrete through internal curing and increases resiliency to physical and chemical attack.
Unlike traditional curing that does not allow water to penetrate much beyond the surface of the concrete, internal curing provides water that is dispersed throughout the depth of the concrete.
-Federal Highway Administration
Field Testing E5® Nano Silica vs Control Samples
Internal curing does not affect the water cementitious ratio, the ratio between water and cement in concrete, which is determined before the concrete is set.
The water from the aggregate will fill the pores of the concrete which helps prevent concrete shrinkage (Bentz and Weiss). Additionally, the increase in hydration increases the reaction of the cementitious materials and therefore improves the performance of the concrete (Federal Highway Administration). Increased hydration also improves the performance of innovative technologies, including nano-silica.
E5® products prevent the bleed water channels that carry contaminates throughout the surface and subsurface. A less permeable substrate protects the concrete matrix from rapid deterioration. The homogenous mixture created by utilizing E5® products results in concrete pavement that is not only resistant to de-icing salts and chemical attack, but also more resistant to steel corrosion, premature failure, adhesion bond failure, and delamination of floor coverings.
DOT Bridge Deck Finish, Minimal Bleed Post Placement.
-
Hydration is THE most critical component to curing concrete. Improper hydration leads to cracking, curling, delamination and many other performance issues over the life cycle of the concrete. Industry statistics show that concrete is typically 10% of the project’s budget, yet causes 80% of the issues faced during and after the construction process.
For years the concrete industry has attempted to create concrete that cures faster and dries harder. Additives that reduce the water and cement content often result in concrete that dries too quickly, resulting in micro cracking and weakened surfaces. Finishers’ work is increased dramatically as they must continually apply water to the surface to combat these issues, therefore destroying the water to cement ratio.
Regulating water while evenly hydrating the cement is the key behind E5® products. Third party ASTM analysis has shown that by controlling the water of transport in the mix design, the concrete becomes significantly stronger in a much shorter period of time. As the concrete strengthens, capillaries in the surface close off and keep unwanted contaminants from entering the slab. By regulating the hydration of the slab concrete is cured naturally from the core outwards.
-
Correct finishing of concrete not only requires the appropriate tools and equipment, but also requires those tools and equipment to be used correctly and with the proper timing based upon environmental variables.
Finish timing can vary based on setting times from load to load. It’s critical to watch the surface of the slab in order to determine the correct timing. Ride-on machines are typically easier to control and run at full speed. However, for the first float pass, it may be necessary to throttle down. If too much mortar is moved to an area where the concrete is too soft or a wet spot is encountered, the floor flatness may be affected when running at full speed. Start at an appropriate speed on the first float pass, and be prepared to throttle down when an area that is soft or wet is encountered.
In addition to the variation in delivered concrete, erratic setting may be caused by the inconsistency of slumps or when additional additives are used. For example, when only part of the concrete is exposed to the sun or only concrete near openings is exposed to wind, those areas will often dry and set faster.
As a baseline for all projects, E5® Incorporated insists all flatwork finishers pass the ACI flatwork finishing course. Following ACI best practices, E5® products give control back to the finisher and provide a workable surface for a longer period of time.
-
Concrete provides structures with strength, rigidity, and resilience from deformation. These characteristics, however, result in concrete structures lacking the flexibility to move in response to environmental or volume changes. Cracking is usually the first sign of distress in concrete. Cracking can occur in both hardened and fresh concrete as a result of volume loss and repeated loading. Cracks occur when the tensile stresses being loaded onto the concrete exceeds its maximum tensile strength. It is important to understand the reasons why cracking occurs, the type of crack formed, and the effects of cracking on structural stability.
Cracking in hardened concrete can result from any one of many causes. These causes include drying shrinkage (which is the main cause), thermal stresses, chemical reactions, weathering, the corrosion of steel reinforcing, poor construction practices, construction and structural overloads, errors in design and detailing, externally applied loads, and poor loading or storage practices. It is important to understand the factors that influence the above causes of cracking in order to reduce and control the effects.
As the results from third party ASTM analysis show, E5® concrete products tackle cracking at its core by properly curing the concrete. Regulating the hydration in concrete stops volume loss and phase change of the water molecules at the surface. With minimal water loss, volume loss is controlled and strength is increased by hydrating a higher percentage of the cement.
-
When the edges or corners of a slab curl up, often at construction joints, it’s caused by concrete at the top of the slab shrinking or contracting faster than concrete at the bottom. This is usually caused by drying shrinkage – water leaves the top surface of the slab faster than it leaves the bottom, creating shrinkage forces that can raise slab edges or corners.
As the results from third party ASTM analysis show, E5® concrete products tackle curling at its core by properly curing the concrete. Regulating the hydration in concrete stops volume loss and phase change of the water molecules at the surface. With minimal water loss, volume loss is controlled and strength is increased by hydrating a higher percentage of the cement.
-
When fresh concrete is placed and compacted, the solids (cement and aggregate) settle. This natural settlement causes excess mix water and entrapped air to be displaced (called bleeding), and the lighter materials migrate toward the surface. If finishing operations start prematurely and close or seal the surface before bleeding is completed, air and/or water are trapped under the densified surface mortar. As concrete hardens, subsurface voids develop where the water or air is trapped. These voids create weakened zones just below the surface that can eventually detach during slab use.
As the results from third party ASTM analysis show, E5® concrete products tackle delamination at its core by properly curing the concrete. Regulating the hydration in concrete stops volume loss and phase change of the water molecules at the surface. Without excess bleed water, the surface of the concrete remains extremely strong, oftentimes stronger than its core.
-
From the initial batch mix, concrete hydrates (or cures) using the water of convenience in the mix. During that process, a large percentage of the excess moisture in the slab typically reaches the surface as bleed water and evaporates. This loss of water is referred to as “volume loss” (as discussed in Cracking and Curling sections). Moisture within a concrete slab follows a number of small pathways, or capillaries, that form as it combines with the initial mix elements – cement, aggregate and sand.
As moisture moves up through these pathways, E5® products adhere to the water molecules and slow them from climbing to the surface. A matrix is then formed in the top layers of the concrete, closing the capillaries. Moisture continues to move within the slab until it reaches a state of balance referred to as equilibration. This is the most critical component of E5® products.
Much of the damage caused by moisture can be prevented, or at least kept at bay for longer periods of time, by means of incorporating Nano Silica. Defense against water and harmful substances is the key behind E5® products. Capillary water absorption of harmful substances leads to surface damage as well as structural damage. Forming a barrier at the surface greatly reduces the amount of water and harmful substances which are absorbed in the slab.
The concrete remains contaminant free as a result and is consequently less susceptible to damage. The most efficient way of protecting concrete is to prevent water and contaminant intake. Affecting concrete at the surface produces positive benefits; even hydration throughout the slab and a tighter, more sustainable concrete slab surface.
-
Concrete is a living, breathing product that continues to change over its life cycle. At first glance concrete may appear rugged and tough, needing no assistance from the surface to maintain its strength and appearance. However, without proper care, concrete can degrade and fall prey to salt, oil, dirt and acidic substances.
Using E5® products ensures concrete is cured correctly and starts on the path to sustainability. A simple regular cleaning schedule will also maintain the shine and seal without the need to use harsh detergents and sweeping compounds.
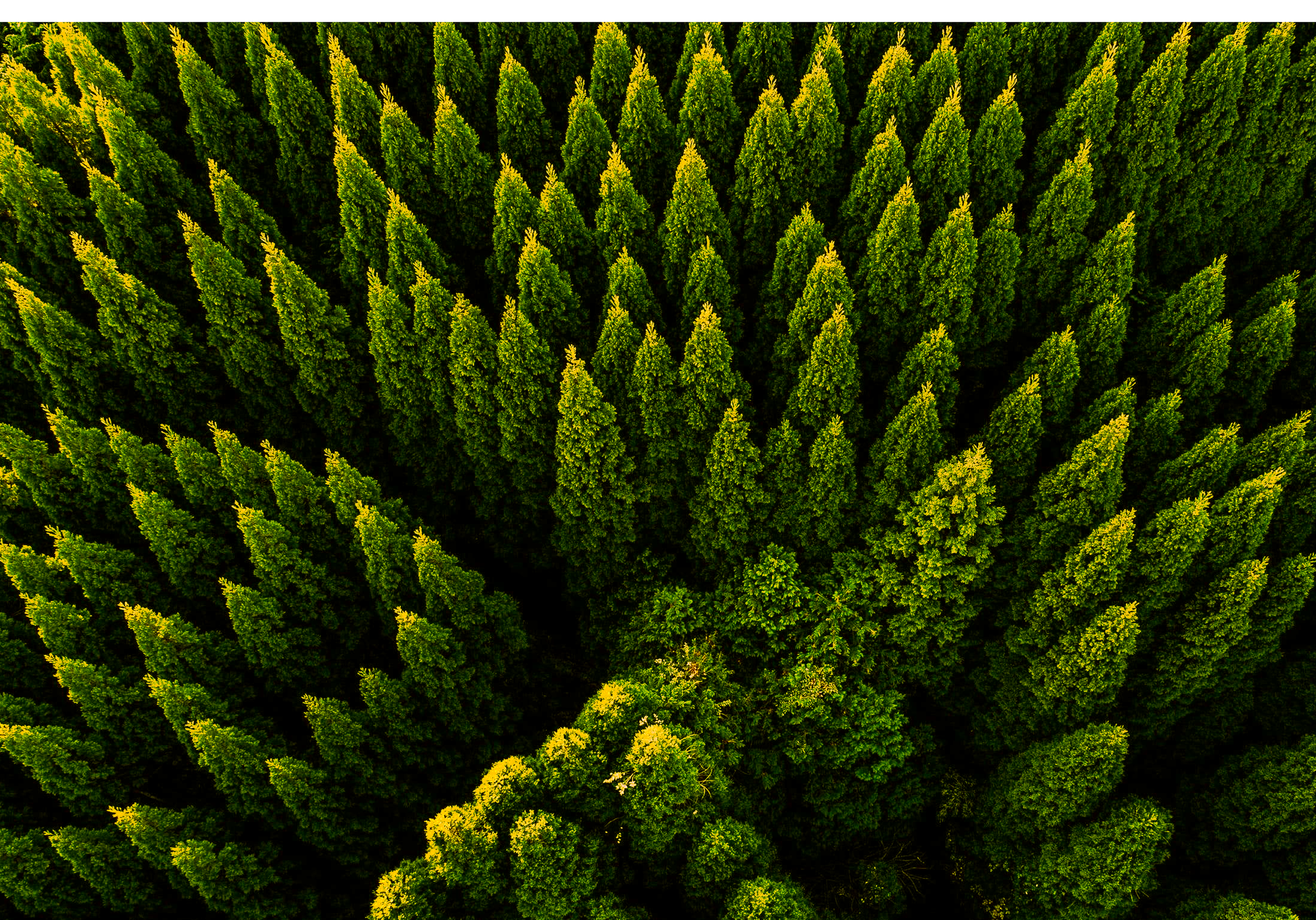